Preventing Weld Undercut: Proven Approaches Every Welder Should Know
Preventing Weld Undercut: Proven Approaches Every Welder Should Know
Blog Article
A Comprehensive Overview to Identifying, Stopping, and Fixing Undercut Welding Problems in Your Welding Jobs
In the world of welding, encountering undercut concerns is an usual difficulty that can endanger the structural stability and general top quality of your welding jobs. Keep tuned as we discover the vital parts of identifying, avoiding, and fixing undercut welding problems, offering you with beneficial understandings and techniques to elevate your welding skills to the next level.
Common Reasons of Undercut Welding
Undercut welding, an usual problem in welding procedures, can be brought on by numerous factors that need to be meticulously determined and resolved to ensure the stability of the weld joint. Among the primary reasons of undercut welding is too much warmth input. When the welding parameters, such as voltage, present, or take a trip rate, are not correctly set, a too much amount of heat can be produced. This excess heat causes the melting and succeeding elimination of the base material along the edges of the weld joint, creating a groove called undercut.
One more common reason of undercut welding is inappropriate welding strategy. Poor control of the soldering iron or weapon, inaccurate angle or distance between the lantern and the work surface, or irregular traveling rate can all add to the development of undercut. Furthermore, using the wrong welding consumables or electrode size for a particular joint setup can result in undercut issues. Identifying these origin and applying restorative steps is vital in preventing and correcting undercut welding problems in welding tasks.
Identifying Undercut in Welds
To determine undercut precisely, appropriate illumination and magnification tools are important to examine the weld joint completely. Using tools such as a welding gauge or a magnifying glass can assist in detecting even the tiniest undercut imperfections. Furthermore, running a finger or a finger nail along the weld joint can often expose undercut, as the surface area may really feel unequal or have a dip where the undercut exists.
Safety Nets for Undercut
Having a deep understanding of the reasons for undercut in welds enables the application of effective preventive procedures to keep weld top quality and stability. One vital safety net is appropriate weld joint preparation. Ensuring that the sides are clean, free of impurities, and appropriately beveled can substantially decrease the chance of undercut (Preventing weld undercut). In addition, choosing the suitable welding criteria, such as voltage, current, and take a trip speed, is important. These setups must be maximized to stop extreme heat input, which can bring about undercut development.
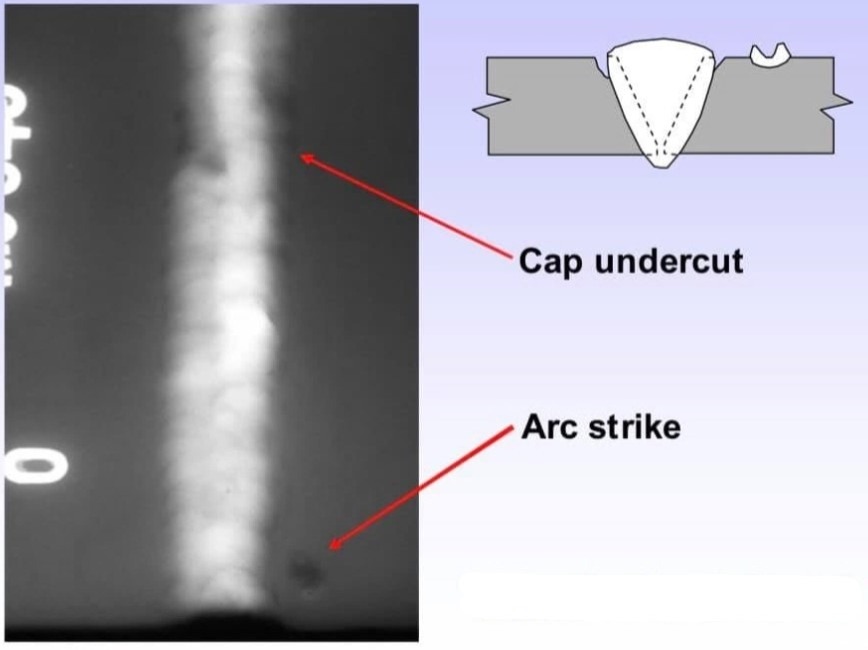
Techniques for Fixing Undercut

To attend to undercut problems efficiently, welders can use details techniques aimed at remedying the flaw and bring back the honesty of the weld joint. One strategy is to change the welding criteria, such as the voltage, present, and take a trip rate, to make certain appropriate heat input and blend. Increasing the welding present or minimizing the travel speed can help load in the undercut. Additionally, altering the welding technique from a press to a drag or vice versa can also aid reduce undercut.
One more strategy is to use a weaving movement while welding to make certain proper sidewall fusion and fill in the undercut. By oscillating the welding arc from side to side within the weld joint, the welder can transfer extra filler material into the undercut locations, efficiently getting rid of the defect.
In addition, grinding out the undercut and rewelding the joint can be a viable option for extra severe undercut concerns - Preventing weld undercut. This procedure entails removing the undercut section, preparing the base metal, and after that rewelding the joint with proper welding specifications and strategies to stop undercut from persisting
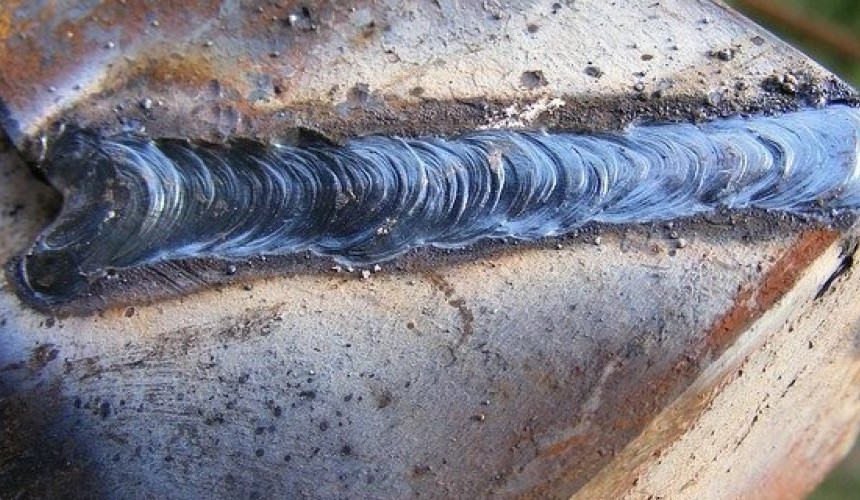
Professional Tips for Avoiding Undercut
Utilizing appropriate welding strategies and maintaining control over essential welding criteria are essential approaches for welders aiming browse this site to stop undercut in their weld joints. In addition, picking the ideal welding process and filler steel for the specific application can assist stop undercut. Maintaining a regular traveling rate throughout the welding process is another crucial suggestion to avoid undercut.
Final Thought
Finally, identifying, avoiding, and dealing with undercut welding troubles in your welding tasks is crucial for guaranteeing solid and long lasting welds. Preventing weld undercut. By understanding the common root causes of undercut, being able to determine it in welds, implementing preventative procedures, and using correct techniques for repairing undercut, you can stay clear of prospective issues and produce top notch welds. Following expert pointers for staying go now clear of undercut can aid you improve your welding skills and create far better cause your jobs
Undercut welding, a common concern in welding processes, can be created by different aspects that need to be thoroughly determined and dealt with to ensure the honesty of the weld joint. In addition, running a finger or a fingernail along the weld joint can often expose undercut, as the surface might feel uneven or have a dip where the you can look here undercut exists.
Utilizing correct welding methods and maintaining control over key welding criteria are vital techniques for welders intending to protect against undercut in their weld joints.In conclusion, identifying, stopping, and repairing undercut welding problems in your welding jobs is essential for ensuring solid and durable welds. By understanding the usual causes of undercut, being able to recognize it in welds, executing preventive steps, and using appropriate techniques for taking care of undercut, you can avoid potential problems and develop premium welds.
Report this page